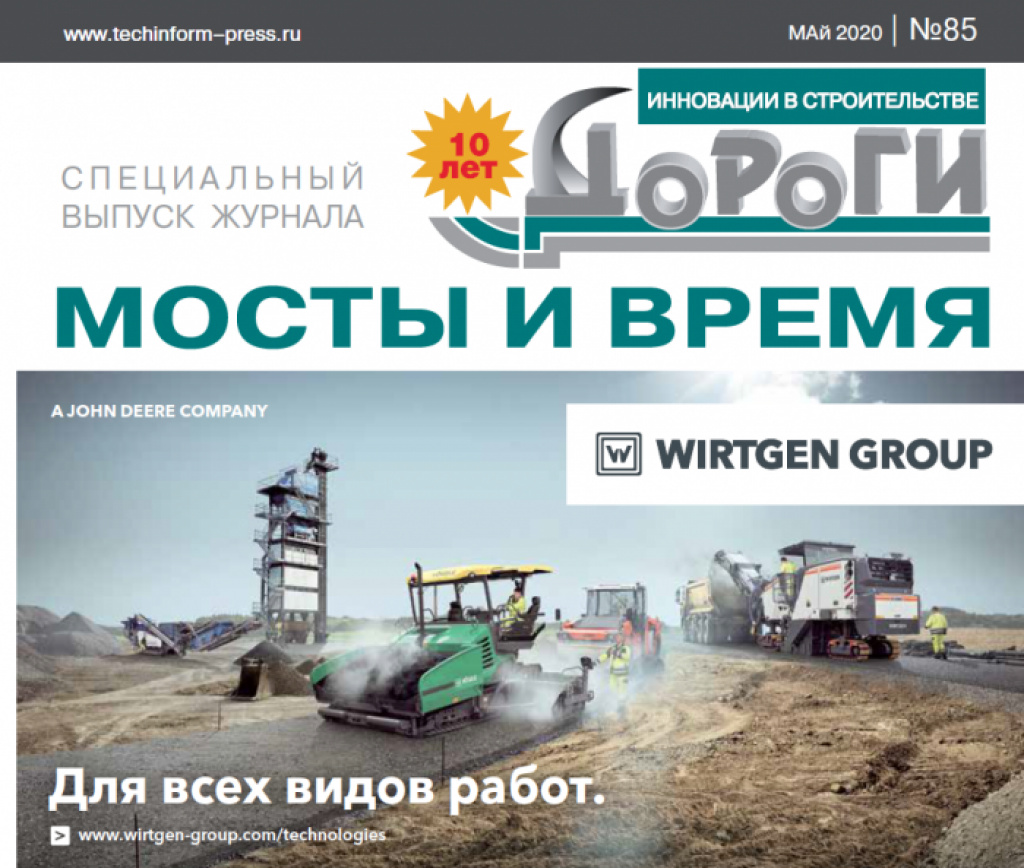
АКТУАЛЬНОСТЬ ВОПРОСА
Дифференциация условий работы сооружений транспортной инфраструктуры диктует необходимость формирования в дорожной отрасли новых подходов к проектированию металлоконструкций в части сохраняемости эксплуатационных свойств под воздействием агрессивных атмосферных факторов. В этом направлении положительный эффект может дать широкое внедрение мостовых конструкций из атмосферостойкой стали.
Здесь следует напомнить, что, по сути, она не является новшеством. Первая такая сталь, кортеновская, разработана в 1930-х гг. в США. В настоящее время металлоконструкции из атмосферостойкой стали широко распространены в США, Японии и странах Европы.
Несмотря на то, что такие решения могут быть несколько дороже традиционных, плюсы их применения очевидны: суммарные затраты жизненного цикла оказываются существенно ниже в сопоставлении с конструкциями из углеродистых сталей с защитными антикоррозионными покрытиями. Например, использование неокрашенной низколегированной стали позволяет исключить расходы как на первоначальную окраску, так и на восстановление покрытия в процессе эксплуатации
моста из обычной конструкционной стали [1]. Однако в отечественной практике строительства подобные металлоконструкции (в частности, из 14ХГНДЦ) до сих пор
не нашли широкого применения.
РЕТРОСПЕКТИВА ОТЕЧЕСТВЕННОГО ПРИМЕНЕНИЯ
В 1980-е гг. в соответствии с программой исследований по проблеме «Создание атмосферостойкой стали типа Кортен для использования в мостовых конструкциях» в ЦНИИЧермете по рекомендации ВНИИЖТа была сделана 21 опытная плавка из стали базового химического состава 14ХГД, которую оптимизировали по никелю, цирконию и церию. При этом содержание фосфора ограничивалось величиной 0,04%. Образцы одновременно испытывались на АКС Дебальцево и АКС Москва-3.
На основании исследований для дальнейшего промышленного опробования выбраны стали марок 14ХГНДЦ и 14ХГНМДЦ. В 1988 году творческий альянс ВНИИЖТа, ЦНИИЧермета и МК «Азовсталь» разработал первый отечественный документ на атмосферостойкие стали — ТУ 14-1-4519-88 для марок 14ХГНДЦ и 14ХГНМДЦ.
По этим техническим условиям для Воронежского мостового завода были изготовлены две промышленные плавки 14ХГНДЦ [1-3].
Первый опыт применения состоялся на железнодорожных объектах. В 1989–1990 гг. в трех различных регионах нашей страны — на Юго-Восточной ж. д. (мост через р. Ворона), на Южно-Уральской ж. д. (мост через р. Камышлы-Аят) и на Восточно-Сибирской ж. д. (мост через р. Снежная у берега оз. Байкал) — установлены три пролетных строения длиной 55 м, изготовленные Воронежским заводом из стали марки 14ХГНДЦ. Все они успешно эксплуатируются до сих пор без окраски.
Результаты обследования в 2010 году показали удовлетворительное состояние металлоконструкций [1, 3].
Опыт исследований позволил институтам «ВНИИЖТ», «ЦНИИчермет», «ЦНИИС» и металлургическим комбинату «Северсталь» (г. Череповец) разработать технические условия ТУ 14-1-5355-98 «Прокат толстолистовой атмосферостойкий из стали марки 14ХГНДЦ для мостостроения», ТУ 14-105-629-99 «Прокат сортовой и фасонный из атмосферостойкий стали 14ХГНДЦ», ТУ 14-105-656-2000 «Прокат листовой из атмосферостойкий стали 14ХГНДФ для изготовления железнодорожного крепежа» [3, 4].
Волгоградский завод в 2001-2003 гг. из стали 14ХГНДЦ (Ф) изготовил около 5 тыс. т ригелей жестких поперечин, применявшихся при электрификации участка Карамыш — Петров Вал — Котельниково — Сальск Приволжской и Северо-Кавказской ж. д. На участке Залари — Головинская и ст. Тайшет Восточно-Сибирской ж. д. установлено 140 ригелей; на участке Свиягино — Ружино — Губерово Дальневосточной ж. д. — 597 ригелей жестких поперечин. В настоящее время в эксплуатации находятся не менее 12 тыс. т неокрашенных несущих конструкций контактной сети из атмосферостойкой стали 14ХГНДЦ [4]. В 2006 году ЦНИИС разработал альбом «Рабочие чертежи № 6226И «Металлические опоры контактной сети и стойки жестких поперечин из гнутых профилей (переработка проекта 0351.1)», предусматривающий применение стали марки 14ХГНДЦ.
ВНЕДРЕНИЕ В ПРАКТИКУ АВТОДОРОЖНОГО МОСТОСТРОЕНИЯ
В автодорожном мостостроении до недавнего времени отсутствовали объекты внедрения атмосферостойкой стали марки 14ХГНДЦ. Впервые она была применена на новой автомобильной дороге первой категории М-11 «Нева» на путепроводе на ПК 2565+44,29 (рис. 1) и мосту через р. Шоша на ПК 1260+38 (рис. 2).
Возможность задействовать сталь марки 14ХГНДЦ при проектировании и строительстве автодорожных мостовых сооружений регламентируется ГОСТ Р 55374-2012и СП 35.13330.2011. Основная проблема этих документов заключается в ограничении ее применения в конструкциях с монтажными сварными соединениями. В связи с этим Государственная компания «Автодор» совместно с ОАО «Уральская сталь» и Головным аттестационным центром сварочного производства (ГАЦ «Мосты») Филиала АО «ЦНИИС» НИЦ «Мосты» разработала СТО АВТОДОР 2.19-2015 [5], в котором отражены основные требования к конструкциям пролетных строений мостовых сооружений из атмосферостойкой стали марки 14ХГНДЦ в части проектирования, заводского изготовления, монтажной сварки и приемки работ.
Важно отметить, что своевременная стандартизация ряда технологических особенностей производства работ с применением упомянутой стали позволила сформировать и апробировать перечень важных показателей, строгое соблюдение которых позволит создавать высокопрочные и устойчивые пролетные строения дорожных транспортных сооружений со снижением первоначальных затрат на 5–10%, а эксплуатационных — на 30%. Обеспечение качества сварки имеет особое значение: сварные соединения являются неотъемлемой частью металлического пролетного строения и гарантируют его равномерно-распределенную работу.
КРИТЕРИИ КАЧЕСТВА СВАРНЫХ СОЕДИНЕНИЙ
Швы заводских и монтажных сварных соединений автодорожных пролетных строений из стали 14ХГНДЦ должны обладать прочностью и коррозионной стойкостью не ниже, чем основной металл. Помимо этого, сварные соединения в соответствии с СТО АВТОДОР 2.19-2015 [5] должны соответствовать следующим критериям:
1) иметь гладкую или равномерно допустимую чешуйчатую поверхность с плавными переходами к основному металлу, без наплывов и не допускаемых подрезов;
2) в многопроходных швах облицовочные валики должны перекрывать друг друга на 1/3 ширины, а глубина межваликовых впадин не должна превышать 0,5 мм для швов, расположенных поперек основного усилия, и 1,0 мм — для швов, расположенных вдоль усилия;
4) все кратеры должны быть вырезаны и заварены;
5) замыкание («закольцовку») угловых швов для обеспечения их герметичности допускается выполнять катетом 4 мм с допуском +2,0, –0 мм с учетом указаний п. 6.45 СТО АВТОДОР 2.19-2015, если иное не указано в чертежах КМ;
6) все свободные кромки сварных конструкций автодорожных мостов, путепроводов и эстакад из стали 14ХГНДЦ, в том числе после срезки выводных планок и зачистки торцов швов, следует скруглять радиусом не менее 0,3 мм;
7) усиления на концевых участках заводских и монтажных стыковых швов, выходящие на свободные кромки, должны быть обработаны шлифмашинкой заподлицо с основным металлом на длине не менее 50 мм;
8) при пересечении угловым швом монтажного стыкового шва усиление стыкового шва должно быть зачищено заподлицо с основным металлом на длине ≈100 мм в зоне пересечения швов;
9) по всем зонам пересечений и примыканий стыковых швов (зоны «крестов» и «полукрестов») их усиления с лицевой и обратной сторон на длине по 150 мм в каждую сторону следует зачистить шлифмашинкой заподлицо с основным металлом;
10) на конструкциях не должно быть ожогов основного металла сваркой; выявленные ожоги должны быть зачищены абразивным кругом до полного удаления следов ожогов;
11) в сварных стыковых соединениях, выполненных односторонней автоматической сваркой под флюсомс МХП на стекло-медных подкладках, допускаются «подмывы» по линии сплавления обратного валика шва с основным металлом на глубину до 1,0 мм, при этом радиус в дне «подмыва» составляет R ≥ 2,0 мм, что обусловлено всем комплексом конструктивно-технологических особенностей сварки стыковых соединений на этом типе медных подкладок; в тех единичных случаях (при нарушении технологии сборки и сварки таких стыков), когда глубина «подмыва» более 1,0 мм, последний следует заварить ручной дуговой сваркой и обработать затем шлифмашинкой.
При несоблюдении хотя бы одного из требований сварные швы подлежат ремонту до проведения ультразвукового контроля и затем повторному визуально-измерительному контролю.
При неразрушающем контроле качества швов оценивают наличие, число, характер и размеры поверхностных и внутренних дефектов.
РЕЗУЛЬТАТЫ ИСПЫТАНИЙ
Примеры монтажных швов на автодорожных сооружениях представлены на рис. 3, 4. При проведении испытаний осуществлялся визуальный контроль сварного соединения на наличие недопустимых наружных дефектов или некачественной подготовки. Шероховатость поверхности при механической обработке зон контроля должна быть не ниже Rz40 по ГОСТ 2789. При обнаружении в металле сварных соединений трещин должна быть установлена их протяженность и глубина с помощью ультразвуковой
дефектоскопии (УЗД).
Важно отметить, что согласно требованиям нормативно-технической документации и во избежание необратимого влияния некачественных сварных швов на прочность и устойчивость конструкции пролетного строения исправление дефектного участка допускается не более двух раз, так же при условии недопущения образования дополнительных дефектов в результате их механической обработки и проверки.
В процессе возведения сооружений в рамках строительного контроля специалисты ООО «Автодор-Инжиниринг» осуществляли оценку качества заводских и монтажных сварных соединений ультразвуковой дефектоскопией (УЗД) в соответствии с методами ультразвукового контроля (УЗК) ГОСТ Р 55724-2013 и требованиями СТО-ГК «Трансстрой»-005-2007 [4]. Применялся дефектоскоп УД 2-70.
По результатам проверки 54 швов на левом и правом пролетном строениях недопустимые дефекты не обнаружены. Параллельно специалисты АО «ЦНИИС» провели независимые контрольные испытания сварных технологических проб. Результаты показали, что технология выполнения сварочных работ, режимы сварки, оборудование и материалы обеспечивают получение механических свойств сварных соединений обычного исполнения, в соответствии с требованиями нормативной документации для конструкций сварных пролетных строений стальных мостов. Химический анализ металла шва подтвердил, что он по химическому составу близок стали 14ХГНДЦ и, следовательно, обеспечивает атмосферную коррозионную стойкость сварных швов на уровне основного металла.
Учитывая технологическую специфику применяемого материала, значительный объем и ограниченные сроки производства работ и, как следствие, требуемую высокую производительность смен, все-таки не удалось избежать незначительных отклонений показателей качества сварных монтажных соединений. Все дефекты, выявленные в результате операционного и приемо-сдаточного контроля, были устранены. Общие и местные остаточные деформации исправлены термической и термомеханической правкой.
Основываясь на результатах проведения входного, инспекционного, а также приемочного контроля, можно с уверенностью заключить, что на всех этапах строительства сотрудники ДТФ «Мостоотряд-90», подрядной организации ПАО «Мостотрест», показали высокий уровень профессионализма.
ЗАКЛЮЧЕНИЕ
Опыт применения мостовых металлоконструкций из атмосферостойкой стали 14ХГНДЦ показывает широкие перспективы для их внедрения в практику дорожно-транспортного строительства. При этом надлежит учитывать параметры атмосферы по ГОСТ 15150.
Представляется необходимым в процессе эксплуатации таких мостовых сооружений предусматривать мониторинг стальных поверхностей на предмет наличия отслаивающихся продуктов коррозии и уменьшения толщины проката. Одновременно пристальное внимание следует уделять состоянию сварных монтажных соединений.
Литература
1. Конюхов А.Д., Шуртаков А.К., Харчевников В.П., Шелест А.И., Воробьева Т.Н. Мосты из атмосферостойкой стали // Вестник ВНИИЖТ. —
2011. — №4. — С. 16-20.
2. Конюхов А.Д. Коррозия и надежность железнодорожной техники. Москва: Транспорт, 1995. — 174 С.
3. Шелест А.И., Кручинкин А.В., Конюхов А.Д. Защита металлических конструкций от атмосферной коррозии // Транспортное строитель-
ство. — 2013. — № 1. — С. 8-10.
4. СТО-ГК «Трансстрой»-005-2007 «Стальные конструкции мостов. Технология монтажной сварки». Москва, ООО «Группа компаний «Транс-
строй», 2007.
5. СТО АВТОДОР 2.19-2015 «Стальные конструкции мостовых сооружений. технология сварки пролетных строений из атмосферостойкой
стали марки 14ХГНДЦ» (утв. приказом Государственной компании «Автодор» от 18.12.2015 № 291).